Table of Contents
NON-CONTROLLABLE VARIABLES
SOIL CONDITIONS
Among the operating conditions that are impossible to select or modify is the soil conditions, which cannot be modified because the profitability of the operation would be extremely high. Therefore, it is considered the most extreme uncontrollable variable. The Excavator operator’s expertise will be necessary to be able to carry out the tour in such a way that the Excavator undercarriage is exposed to the least possible wear.
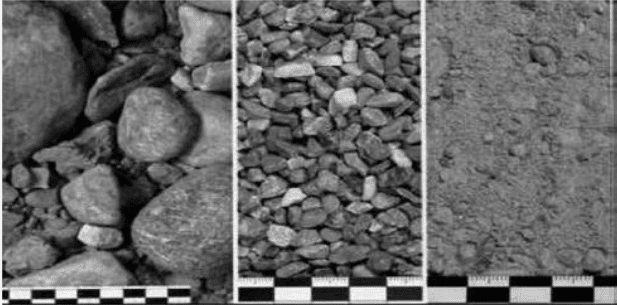
ABRASIVITY
Abrasiveness is a soil condition that represents a very big problem because it causes on the equipment, and it is also difficult to quantify the effect of abrasiveness.
The moisture contained in a soil plays a decisive role in abrasiveness, because the moisture produces an acceleration of the speed at which the particles adhere to the metal surface, as well as their transport, which generates greater wear. Abrasion usually occurs in different areas of the undercarriage, some attack the bushings, shoes, links, and rollers. There is no simple way to quantify the degree of damage caused by the abrasiveness of the terrain. As a rule, the link is used to be able to compare the abrasive effects relative to it. It is generally used as the base component when comparing the useful life of the rest of the components to the abrasive conditions of the soil.
ABRASIVITY CLASSIFICATIONS
- High: Highly saturated wet soils have many hard, angular, or sharp sand particles.
- Moderate: Slightly or temporarily moist soils that contain a low proportion of hard, angular or sharp particles.
- Low: dry soils or rocks that contain a very low proportion of hard, angular sand particles or rock chips.
IMPACT
The impact depends on factors such as the weight of the machine and the speed are classified into:
IMPACT TYPE CLASSIFICATIONS
- Height – Nearly impenetrable hard surfaces with constant exposure to 6 inches (15 cm) or more “bumps”.
- Moderate: partially penetrable surfaces with constant exposure to small bumps.
- Low: fully penetrable surfaces that allow full support for the shoe plate, with almost zero exposure to potholes.
The most relevant effect of the impact is evident at the structural level because it causes serious problems, such as cracking, bending, breaking, chipping, splintering, greater risk of tipping, among others.
In general, in larger machines the useful life is not as affected by impact problems compared to smaller machines in which the impacts could reduce the useful life in a very short time due to the difference in robustness between equipment.
PACKING
The packing describes any condition in which the material underfoot sticks or clumps between each of the undercarriage components. They generally have 2 effects:
- First, it can be prevented by mating the parts correctly to each other, otherwise this can cause interference, exaggerated loads, and a high rate of wear. A clear example of this effect occurs in sprocket tooth packing and packing between shoes and bushings, which causes the teeth to incorrectly couple to the bushings.
- The second general effect of the gasket is that it generates more wear because the abrasive material adheres to the surfaces, wearing them down. A clear example of this is a sand and clay mixture packed around the idlers, carrier and chain rollers that causes constant abrasion when these components encounter the chain links. The result is like that of a sharpener or polisher. Parts subjected to this effect are usually polished to smooth the surface.
Packing materials cover a large number and extend far beyond the clay and mud that are best known and commonly associated with the operation of machines. The following bill of materials may result in one or both general effects mentioned above. As might be expected, the moisture content of most of these materials helps determine their adhesion and compatibility. Many soil conditions are made up of various combinations of these materials and the effect can be cumulative.
These types of materials are divided into 2 categories:
- Extrudable: those that can normally be extruded or squeezed between parts when wet.
- Non-extrudable: those that cannot be extruded with the pressures and opening sizes normally available in crawler-type machines.
TYPE OF MATERIALS
1.- Extrudable (wet)
- Sanitary landfill (garbage)
- Silty soils
- Clay soils
- Sandy soils
- Snow and ice
- Metallic minerals (taconite)
- Non-metallic minerals (gypsum)
2.- Non-extrudable
- Sanitary landfill (garbage)
- Branches, twigs, and bushes
- Stones, rocks, and gravel
- Demolition debris
- Grass-like materials
Usually, the packing effect is impossible to control, however there are some modifications and options, such as the use of additional accessories, that you can implement on your machine to try to minimize this effect. The modification that is most carried out in the undercarriage involves modifying one of the components, in this case the shoe is modified, because it requires that there be trapezoidal openings so that the packing material is extruded or falls, in this way reducing pressure. These modifications or increases should only be made in the presence of extrudable type materials.
- Trapezoidal openings in shoes: It is recommended that track shoes with trapezoidal openings be used in the presence of extrudable material. These shoes are available for most machines. These shoes are not of the “standard” type because, in the absence of packing, they allow material underneath to enter the system and the service life will be shorter.
- Full Length Track Roller Guards: Not recommended for use in all cases, recommended in cases where rocks can get between the rollers and cause crush damage. Roller guards are not a good option because they tend to keep the packing material in the system.
- Sprockets and segments for mud and snow: Recommended to be used only in the constant presence of soft extrudable packing materials. On any other material, the result will be accelerated outer hub wear due to reduced contact area on the sprocket.
OTHER ENVIRONMENTAL VARIABLES
There are other conditions that may or may not be associated with the soil and its properties.
HUMIDITY
The effects of moisture as contributors to abrasiveness and packing were discussed previously. Moisture in the ground or in the environment can corrode steel and lead to loss of material and accelerated wear. The amount of moisture in the environment increases the corrosive effects of many other chemicals and compounds; both those found in nature and artificial ones, such as sulfur, salt, and fertilizers.
Water in large quantities provides a great benefit by contributing to the elimination of abrasive particles, softening many packaging materials to facilitate their extrusion and finally, diluting some chemical corrosion agents to reduce their effect.
CHEMICAL PRODUCTS
Corrosive chemicals found in nature in addition to man-made compounds can have the effect of “eating” the material, causing increased wear or acceleration in the formation of certain types of cracks. Ironically, most hardened steels are more susceptible to corrosion cracking than softer, unhardened steels. Highly acidic and saline soils can contribute to these effects. Organic chemicals, such as petroleum products, can attack rubber load rings and O-rings on idlers and rollers, causing them to fail.
TEMPERATURE
High temperatures increase the rate at which chemical reactions occur. Extremely high temperatures, such as those found in steel mill slag removal, can damage seals, and soften hardened steels underneath undercarriage parts. Very low temperatures can result in brittle steel, loss of elasticity of the rubber seal and reduction in the flow of lubricant needed in the sealed and lubricated chain, roller, and idlers.
GROUND CONDITIONS
WORKING ON THE HILL
Weight balance is shifted to the downhill side of the machine. This results in an acceleration in the wear rate of those components on the downhill side of the machine. Additionally, wear increases on the sides of the rails, idler rollers and flanges, bushing ends, and grouser ends.
WORKING DOWNHILL
The forward weight balance is changed, it causes quite high wear on the chain rollers and front idlers and on the reverse drive side of the sprocket and bushing.
WORKING UPHILL
Weight balance is shifted towards the rear, causing slightly more wear on the rear chain rollers and idlers and on the front drive side of the sprocket and bushing.
WORKING ON A CROWN
The side of the components closer to the center and its components will withstand heavier loads, resulting in increased wear on the inner wear surface of links, rollers, idler treads, and grouser ends. In extreme cases, the internal contact surfaces of the bushing to the pinion can be affected and suffer increased wear.
WORKING IN A DEPRESSION
It causes the loads to be transported by the side of the components that is on the outside of the machine. This results in increased wear on the outer wear surface of links, rollers, idler treads, and grouser ends.
PARTIALLY CONTROLLABLE VARIABLESVARIABLES
Among many variables that affect the life of the undercarriage, there are some that can be partially controlled to some extent, in some cases they are not clearly independent, but the operator can make decisions to reduce wear on the machine. They are usually known as the “in operation” variables, but they do not refer to the soil or its conditions, they depend on factors that can be regulated by the machine operator.
SPEED
The wear rate is directly related to speed because wear occurs as a function of the distance the equipment travels, not just the amount of time it is operating. As speed increases, wear rates increase on all components. Wear rates and impact (structural) effects increase as speed increases as the number of times parts contact each other increases. The wear rates of the link rollers, link carrier roller, link roller and hub sprocket increase because of the increased impact between these parts. Shoe and grouser wear rates increase due to increased ground contact. High speed reverse has a particular effect on the wear rates of the bushing-pinion contacts due to the design of the track. It is recommended that when the machine is not being operated the transport speed is low. In addition to avoiding the change of direction and, as far as possible, carrying out a study of how the machine will operate to avoid non-productive setbacks.
TURNING
Wear rates increase when turning. When rotating the interference loads between the links and rollers, and the links and idlers, are increased, it occurs on the sides of the rails and on the flanges of rollers and idlers. In the same way, the backward turns can generate an acceleration in the wear of the hub sprocket, which would not occur of such dimension if it were turned forward. If the turns are made in only one direction, they will cause the tracks on one side to suffer a more accelerated wear, for which it is recommended to change the most worn side at the middle of its useful life.
SLIPPING TRACKS
The level of wear on all components increases as the operation proceeds and the track begins to slip. Especially the track shoe grabs are affected when the tracks slip because there will be more slip between the grapple and the ground. When the soil conditions are resistive, there is an increase in the loads.
It must be considered that the components on the loaded side of the machine will wear out at a higher speed. The speed of wear also depends on the power applied. More slippage and packing will occur on the loaded side, which also contributes to increased wear. Putting more loads and packing on one side of the machine can cause the wear rate on that side to be even double that of the other side. You can try to minimize the effects if you make a change of the components from one side to the other, this way at some point both sides will have the same amount of wear. It is recommended as a rule of thumb that it should be done when the link and / or rollers reach half their potential service life on the most loaded side.
FREQUENTLY ASKED QUESTIONS (FAQ SECTION)
What types of equipment will I use to measure undercarriage component wear?
There is very modern equipment that is the most indicated to be able to provide a fairly accurate indicator of wear, this measures the thickness of any of the components using high frequency waves that will be sent through the material of the component to be measured. The time that elapses between sending the wave and receiving it is what allows quantifying the thickness of the component and in the same way comparing with the original component to know how worn the component is.
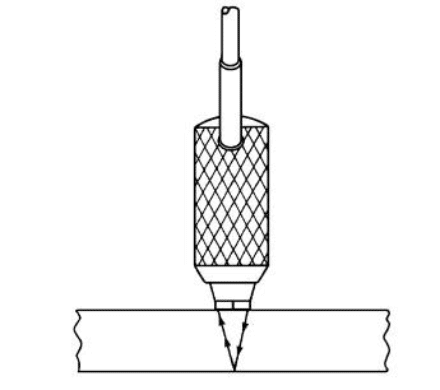
0 Comments