Table of Contents
COMMON PRACTICES
The undercarriage is one of the most important elements of the excavator, especially due to its high cost and its importance in the operation of the equipment, it is necessary to follow the manufacturers’ recommendations so that the effect of equipment wear is minimal, to Here are some operating tips that are recommended to be clearly explained to the operators in a training to optimize the life of the track chains and in general of the undercarriage:
Make Wider Turns
– Sharp turns or unexpected machine rotation results in fast wear and increases the chance of yaw.
Minimize operation on slopes:
When operating machinery, there are times when it is unlikely to decide the route to be used, therefore, in many cases it is required to operate on slopes, hills or hills. Care must be taken with respect to how the machine moves, up or down, it must be ensured that the drive motor is correctly positioned to minimize general wear on the chains. The motor should be positioned towards the rear of the machine to make it easier to maneuver on a slope or hill.
Avoid operating on unstable terrain:
Materials such as asphalt, rough concrete, and other abrasive terrain can cause track damage.
Minimize turns:
Train operators to avoid unnecessary turns, wide turns required and less aggressive with equipment. Chain spinning can cause wear and tear and lower overall productivity.
Avoid operating the track in reverse:
This operation triples the number of pins and bushings that are under steel-to-steel contact, load, and movement, because the transmission tension is generated from the sprocket, on the carrier roller, around the front pulley, down to the ground. On the other hand, the only links in the chain subjected to drive tension when operating forward are the few between the bottom of the sprocket and the first claws that bite into the ground.
Study the operation to be carried out:
The wear suffered by the chains is directly proportional to the distance and speed, so you must plan your work in such a way that each operation that is carried out is productive and completely necessary.
Use rock guards if necessary:
When working on very large rock terrain use rock guards so that they are easily accommodated between the sprocket teeth and the track bushings or between the track links and the belt of the idler wheel. Rock guards also help guide idlers and rollers when working on steep slopes. But it is advisable to avoid rock guards if you are working under normal conditions. When working on ground or packed surfaces, full-length rock guards will trap material between the chain rollers and links, resulting in a decrease in the life of each item.
As can be seen, the incorrect operation of the equipment can cause many unnecessary expenses that can result in extremely high repair bills, for this reason it is recommended to train the operators since they are directly responsible for following these tips.
MAINTENANCE
It is usually very common for some companies to overlook excavator track maintenance, without considering that the investment in maintenance will save them a much greater expense if the element fails. Below are several things to follow regarding undercarriage maintenance to optimize service life, thereby reducing overall costs. It is necessary to always bear in mind that the preventive maintenance of the undercarriage will allow all the elements of it to be used for as long as possible.
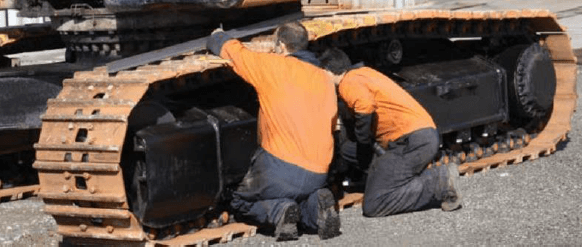
CLEANING
The easiest factor to control is the periodic cleaning of the undercarriage, at the end of the working day the equipment operators must clean all the dirt and debris that accumulated throughout the day on the undercarriage, in Failure to perform periodic cleaning will cause premature wear of the components. It should be considered that proper cleaning will eliminate the debris that causes an increase in the overall weight of the undercarriage, by eliminating the extra weight, an adequate use of fuel is produced and a fuel saving plan can be generated.
Among the most common materials that must be cleaned are organic and inorganic compounds. The organic classification includes hydrocarbons such as grease and fuel residues. In addition to vegetation that may exist on the ground and any type of insects or even birds. On the other hand, inorganics are made up of mineral compounds such as area, gravel, and dust.
There is a mixed category, which is a mixture between organic and inorganic, for example, the soil which is basically a decomposing organic compound mixed with static inorganic compounds, in addition, the soil is usually very polluted. Due to this, the earth is one of the most difficult materials to clean in any type of machinery.
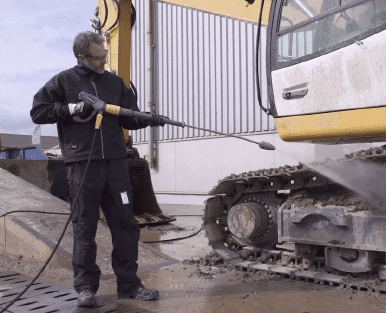
CLEANING METHODS
There are equipment manufacturers that make undercarriage designs in such a way that it is easier to clean the carriage from the track, this design allows mud, dirt, and debris with the help of gravity to fall to the ground, preventing it from accumulate inside the undercarriage. However, in the scenario of excessive dirt and debris, operators are advised to use hand shovels and pressure washers to ensure that the undercarriage is in optimal operating condition. Within the maintenance area there is a category of companies that specialize in cleaning heavy mobile machinery, they are responsible for extracting dirt and debris from the excavator.
For a simple and effective daily maintenance, a shovel can be used to clean the dirt from the upper rollers and around the sprockets, it is planned daily to avoid that at low temperatures at night the material can freeze and dry, generating that the next day they get stuck, a visual inspection is carried out at the end of the day to make sure there are no loose components. For the cleaning task, you can look for companies that provide pressure washing services or choose to do the cleaning yourself, so you must know the most efficient and safe way to clean it. There are many different methods, they may differ from one another, but regardless of the method chosen, the result must ensure that the equipment is not damaged and that it has been performed efficiently and correctly.
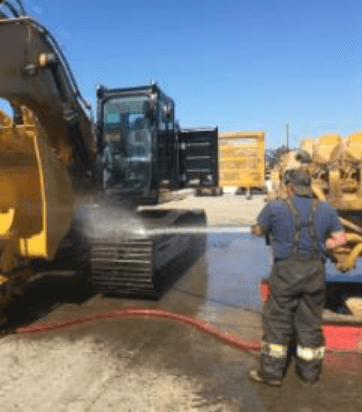
USE OF DETERGENTS / DEGREASERS
If you have neglected the maintenance of the equipment, but want to start a proper maintenance, you should bear in mind that pressure washing is probably not the most suitable option if the maintenance has not been done for weeks or even months. In this situation, the pressure will not be able to clean the equipment properly, especially if there is some type of grease that is part of the dirt.
For the cleaning of industrial machines, water will not be enough, it is very unlikely that cleaning will be effective only using water for cleaning when the equipment is used in construction or agriculture areas it is necessary to use some type of chemical degreaser. In the maintenance industry there are detergents for heavy equipment, which act as surfactant active agents, when mixing water with these detergents the break between the dirt and the surface where it is lodged occurs.
Fat hardens over time, so it will most likely require scraping to remove it. It is relevant to remember that the operating conditions of the equipment also play a very important role when deciding what type of cleaning should be carried out because if there are dry components on the ground, it cannot be removed with high pressure, no matter how high. be the pressure the dirt will not come off. To remove the grease and dry components, a suitable chemical cleaning agent is required, using this procedure the time necessary for cleaning will be longer. To use the proper degreasing chemical, you should consider the local laws and recommendations of the authorities on the handling of these chemicals.
WATER TEMPERATURE
The effect of the water temperature plays an important role in cleaning because if cold water is used, many more resources will be needed, that is, a greater amount of degreaser, in addition to obtaining an acceptable result, it will take much more time to generate if a longer time of the equipment out of operation. This is significant for regions where it reaches very low temperatures in the winter, therefore, the operator must plan maintenance.
The same method for cleaning consists of a pressure washing with hot water, this technology is competent, presses the debris and degreases the machine in a more efficient way, which translates into cost savings since the equipment needs less time to be ready to operate again.
Cold water is quite effective if the correct surfactant is used, and the cleaning time is relatively short. On the other hand, hot water works better on the surfaces of the machine, which makes it possible to remove larger pieces of dirt more easily. Therefore, you can clean either with hot or cold water, considering the resources that you must use in each case.
TRACK SAG
One of the dominant factors that can be controlled to avoid easy wear of the track chain is the sag of the track, although it should be considered that it is not an easy task to maintain the suggested sag as the tension undergoes constant changes, however, there are several tips and steps to reduce the overall cost of the undercarriage.
There are 2 scenarios that would cause the track to malfunction. The first case is when the equipment track is excessively tight, which generally generates wear of the track and consequently of some other elements of the running gear. The second scenario is totally different, it occurs when the track is loose, this can cause the machine to be quite unstable in its operation, it can even slip off the sprocket.
According to what has been explained above, it is concluded that verifying the track sinking conditions should be part of a daily maintenance program. The buckling of the track is usually a specific recommendation of the equipment manufacturer, a reference value that is used in many excavator tracks is 2 inches, the problem is because this tension experiences variations depending on the conditions of the terrain; Therefore, it is necessary to establish steps to be able to manage the sinking of the track.
PROCEDURE TO FOLLOW TO MEASURE THE TRACK SAG
STEP ONE: RAISE THE TRACK
Rotate the upper structure so that the boom is positioned 90 degrees in the direction of travel, put the excavator arm perpendicular, on a surface without unevenness. Use the boom to press against the surface and you can raise the track so that it is suspended at ground level. Operate the equipment so that the rail makes several revolutions to be able to remove the debris that is on the track. Stop the equipment completely.
STEP TWO: MEASURE THE TRACK SAG
Locate the lowest point, using a standard tape measure from the bottom of the rail frame to the top face of the shoe. Using your equipment manual, compare the measured value called “track sag” with the crawler buckling specifications found in your equipment manual.
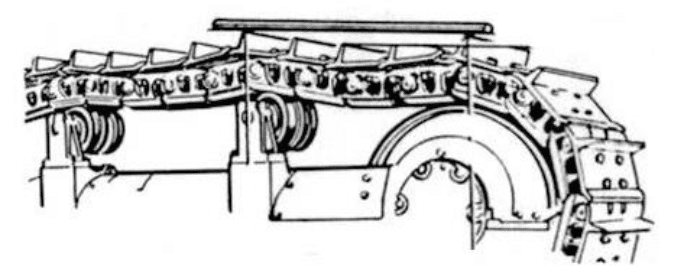
STEP THREE: PREPARE FOR ADJUSTMENT
If the crawler tension is not within the ranges specified in the equipment manual, an adjustment must be made, the operator must remove the cover plate located on the undercarriage frame. When the plate is removed, you can clearly see the track adjusting valve and oiler.
STEP FOUR: TIGHTEN OR LOOSEN THE TRACK
The track adjuster is a grease filled hydraulic cylinder used to maintain track tension. If you want to change track tension, add or remove track adjuster grease.
Track settings are normally activated with a grease gun. Use caution and read the manual carefully to avoid pressurized fluid hazards. If the track is too tight, the grease retaining the idler pulley is under extremely high pressure and must be handled with great care.
To tighten connect a grease gun to the grease nipple and add the amount of grease until the guide wheel of the rail extends as recommended in the equipment manual, on the other hand, to loosen the tension of the track, turn the valve little by little track adjustment knob counterclockwise, allowing grease to drain out of the bleed hole, when the track sag value is satisfactory turn the valve counterclockwise to tighten it.
FREQUENTLY ASKED QUESTIONS (FAQ SECTION)
How often is it advisable to perform maintenance?
It is a question that depends a lot on the variables of the terrain and operation, but generally many manufacturers of undercarriages confirm that carrying out correct training to operators saves a lot of money in maintenance, they also agree that a visual inspection and cleaning is enough since all elements are designed to have approximately the same useful life if the equipment is used as the manufacturer recommends.
What is the allowed range of runway sag?
There is no established range, each equipment has a reference value for which it is recommended that the operation manual be reviewed.
0 Comments